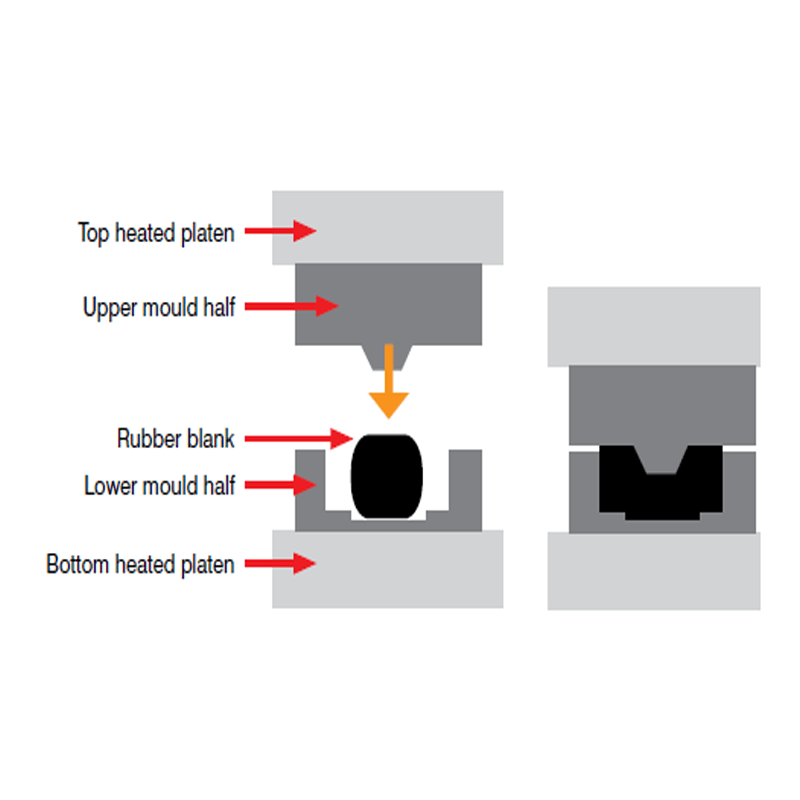
Advantages of Compression Molding
Compression molding offers several advantages over Liquid Silicone Rubber (LSR) injection molding, making it an attractive option for certain applications:
- Faster and more cost-effective tooling: Compression molds are generally quicker and less expensive to produce compared to injection molds.
- Cost efficiency: Compression molds can sometimes be modified for different part revisions, reducing the need for entirely new tooling.
- Flexibility in design: Compression molding tools can be designed as 'family tools,' allowing for different part revisions or designs in each cavity, making it a versatile and efficient process.
- Ideal for small production runs: The relatively simple nature of the technique makes it well-suited for smaller volume production.
- Multiple silicone grades: The process allows for the use of different grades of silicone without the complexity of material changeovers seen in injection molding.
- Cost-effective material options: High Consistency Rubber (HCR) grades of silicone can be molded using compression tools, offering a less expensive alternative to LSR, which requires specialized handling and metering equipment.
- Shorter development time: The process development for compression molding is significantly shorter than for injection molding, allowing for more design iterations in less time.
- No gate vestiges: Since compression molding doesn't require gates, parts are free from gate vestiges, ensuring a clean finish.
Silfusion's Precision Silicone Rubber Compression Molding Solution
At Silfusion, we take pride in delivering top-notch mould for silicone production with a focus on quality and on-time delivery. Our advanced infrastructure is equipped to handle your unique and intricate design requirements efficiently. Utilizing "Rubber Compression Molding" technology, we specialize in producing silicon products in low to medium-order quantities. Our team of experienced professionals will provide expert guidance and support, ensuring you find the perfect solution for your business needs.
Material Expertise: We have extensive knowledge and experience in working with various silicone rubber materials, allowing us to recommend the most suitable material for your specific application. Whether you require high-temperature resistance, excellent electrical insulation, or biocompatibility, we have the expertise to meet your requirements.
Advanced Tooling and Mold Design: Our solution incorporates cutting-edge technology and expertise in tooling and mold design of rubber compression. We leverage CAD/CAM software and precision machining to create high-quality molds that ensure accurate replication of your desired product.
Design Flexibility: With our Precision silicone compression mould Solution, you have the freedom to design and create complex shapes, intricate details, and precise dimensions. We work closely with you to transform your ideas into reality, ensuring that your product meets your exact specifications.
Surface Finish and Aesthetics: Our Precision Silicone Rubber Compression Molding Solution enables the production of parts with superior surface finish and aesthetics. We pay meticulous attention to detail, ensuring that your products not only perform flawlessly but also have an appealing appearance.
In-house capabilities
Not being dependent on outside sources allows us to maintain complete control of every job, ensuring quality products, shorter lead times, on-time delivery, and competitive prices for our customers.
Certificate And Silicone Report: ISO 9001:2015, IATF16949, FDA, ACS, KTW, W270, Biocompatibility
Rubber Compression Molding Process
Once all necessary elements are in place, the vulcanized rubber undergoes compression within prepared molds.
The following outlines the steps in the rubber compression molding process:
1. The mold is preheated and sealed to ensure optimal conditions.
2. Uncured rubber (preform) is placed inside the mold cavity.
3. The mold is then securely closed.
4. Heat and pressure are applied according to pre-set parameters, using programmable logic controls to ensure precise temperature and pressure.
5. Once cured, the mold is opened, and the finished rubber part is removed.
6. Post-molding operations, such as deflashing, inspection, and post-curing, are then carried out to complete the process.
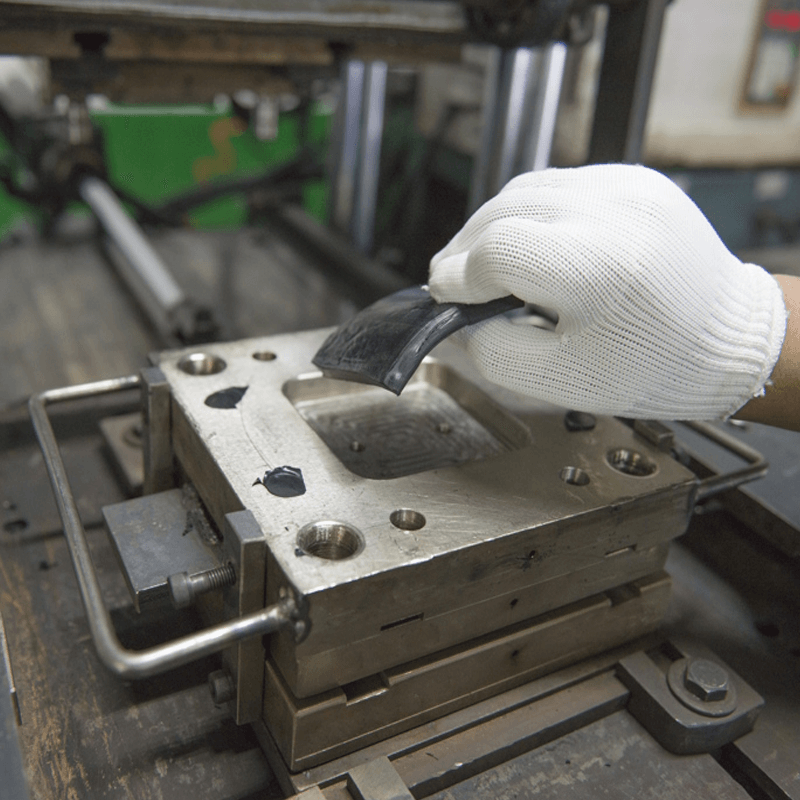
Silicone Compression Tooling
Due to the high elongation properties of High Consistency Rubber (HCR) and Liquid Silicone Rubber (LSR), simple parts with minor undercuts can be easily de-molded using a two-plate compression mold. For more complex geometries, a multi-part compression mold, typically consisting of three or more plates or actions, is required.
At Silfusion, we typically use both aluminum and steel for our silicone compression molds. Aluminum molds offer faster machining and polishing times compared to steel and boast a higher heat transfer rate, which aids in the molding process. This allows us to produce aluminum mold tools in as little as five business days, with the capability to handle up to 10,000 shots. The standard lead time for an aluminum compression mold is 15 business days, although we can expedite delivery to 5 to 10 days for urgent sample projects.
For multi-cavity compression molds, we recommend using steel over aluminum. Steel molds take approximately 20 to 25 days to complete due to the additional time required for machining and polishing.
Industries Utilizing Compression Molding Products
HCR silicone rubber, commonly used in compression molding, is designed to perform in both extreme high and low temperatures, making it ideal for a variety of demanding applications. Industries that rely on compression-molded silicone products include:
- Automotive
- Food and Beverage
- Marine
- Medical and Pharmaceutical
- Aerospace
- Rail and Mass Transit
These sectors benefit from the durability, temperature resistance, and versatility of compression-molded silicone rubber components.
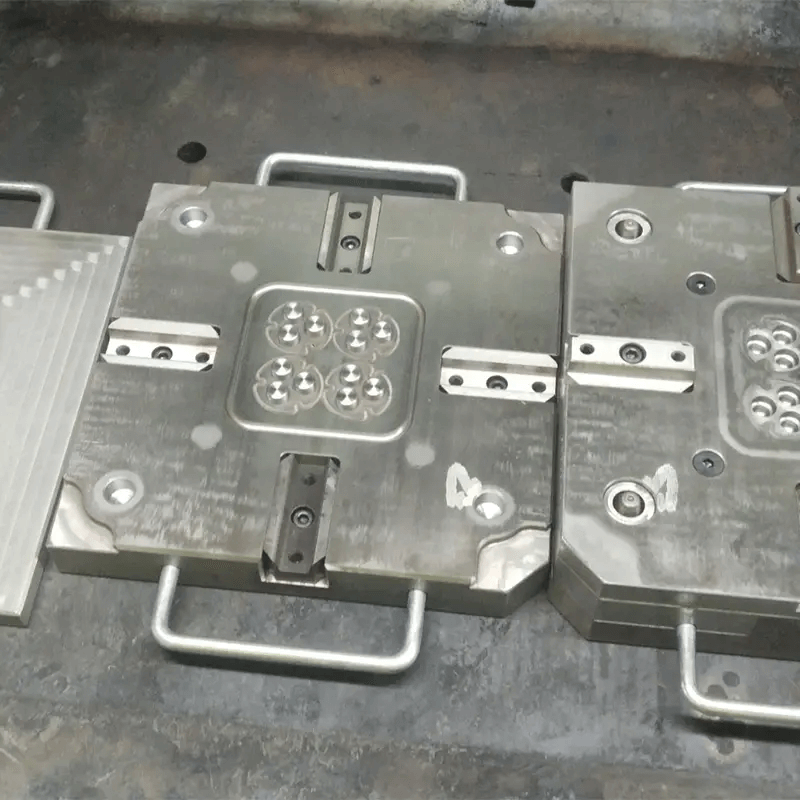
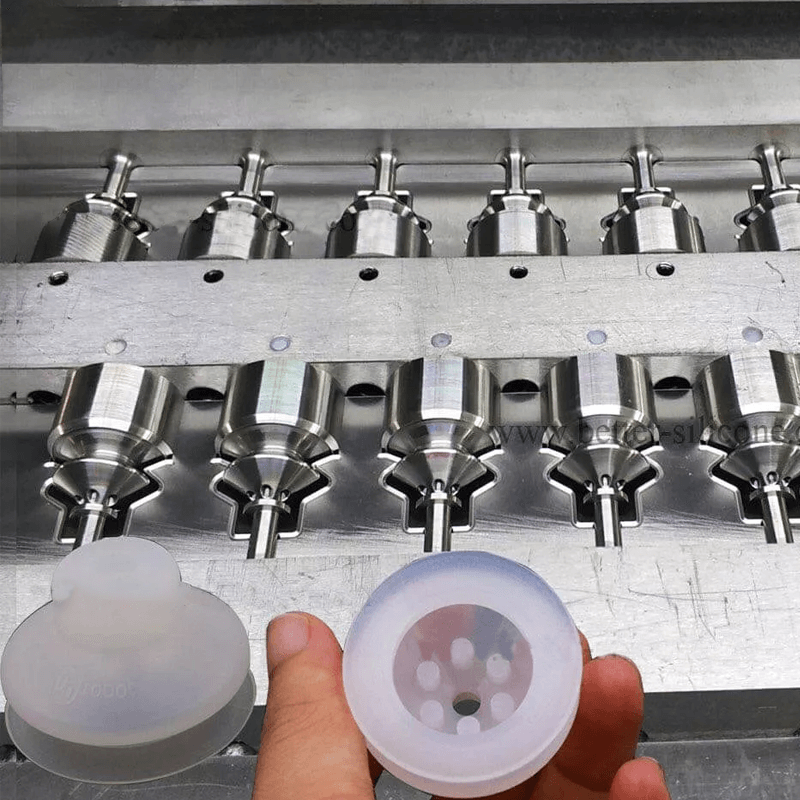
Custom Silicone Compression Molding
With over 20 years of dedicated experience in silicone molding, Silfusion stands as the leading expert in HCR compression molding technologies. Our deep expertise enables us to customize every step of the process to meet your specific needs, elevating your custom innovations to the next level.
As a premier silicone parts manufacturer in China, we proudly serve businesses across the globe. Our advanced capabilities cover the entire spectrum, from design to production. We assist in selecting the ideal HCR grade, optimizing design for manufacturability (DFM), delivering top-tier tooling, supporting high-volume production, and offering comprehensive packaging solutions. Our high-quality HCR components are widely utilized in industries such as automotive and medical.