What Is Plastic Injection Molding?
Plastic injection molding is a highly efficient manufacturing process used to produce a wide variety of plastic parts with precision and consistency. The process begins by melting plastic resin pellets, which are then injected into a precisely designed mold under high pressure. Once the plastic fills the mold cavities, it cools and solidifies to form the final product.
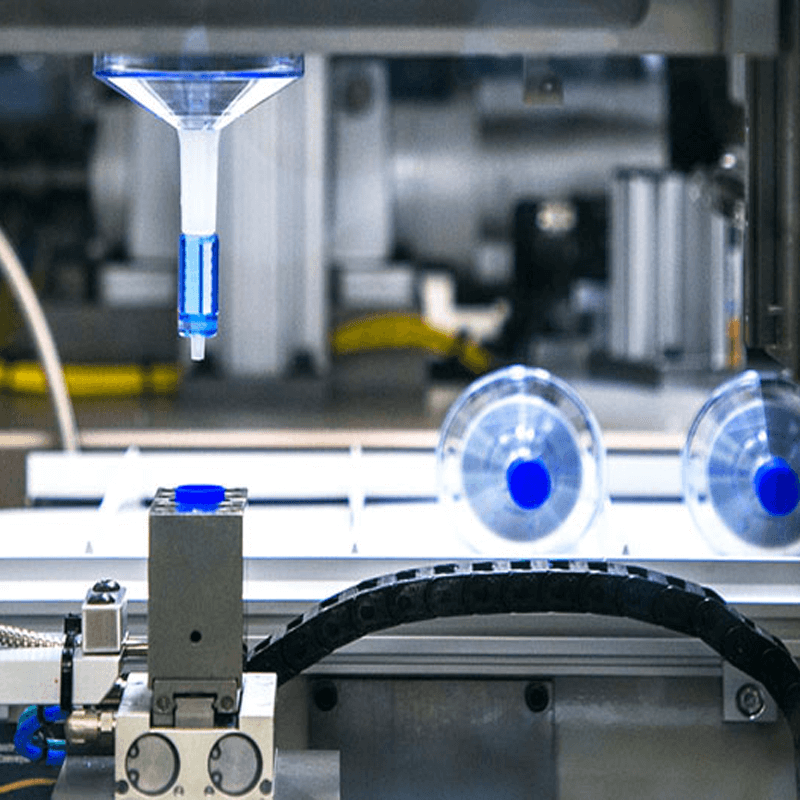
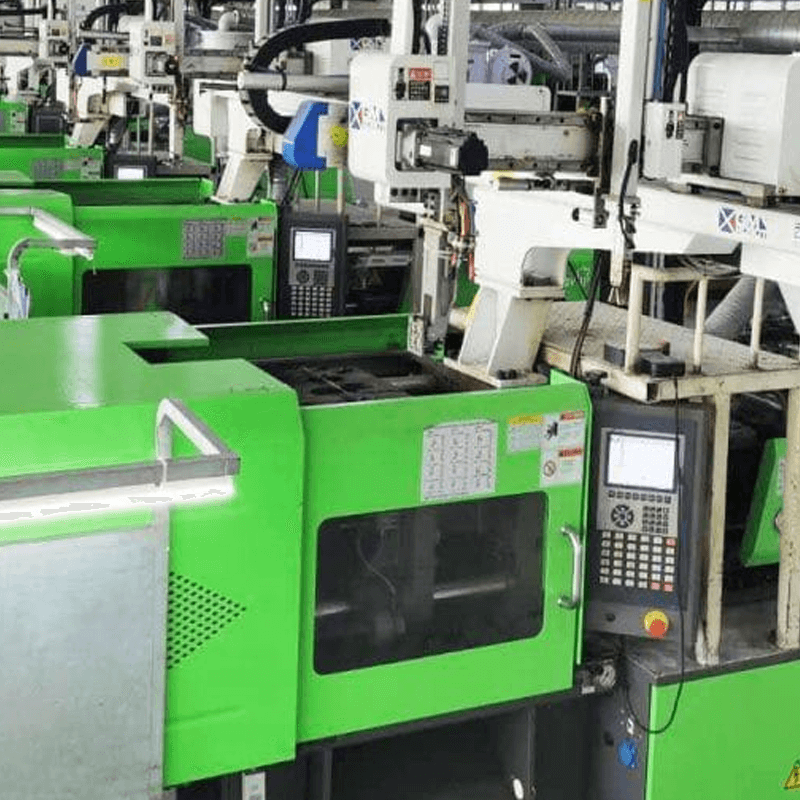
Our Injection Molding Advantages
Silfusion provides comprehensive injection molding services to global clients, leveraging our team of skilled and diverse designers and engineers to deliver cost-effective solutions. Our robust management system guarantees the reliable delivery of high-quality products, tailored to meet your need for swift turnaround times.
Exceptional Quality
Rapid Turnaround
Versatile Applications
Cost Efficiency
Custom Plastic Injection Molding Materials
Many companies utilize injection molding to manufacture high-volume, complex components. This process provides numerous advantages, including enhanced productivity and lower unit costs. To assess whether custom plastic injection molding services are suitable for your application, it's essential to understand the variety of injection molding materials available. Silfusion offers a comprehensive range of these materials.
PC (Polycarbonate)
Polycarbonate (PC) is a versatile, lightweight plastic with a glass-like appearance, commonly used across various industries. Known for its impact resistance and ability to retain fine details, PC is ideal for applications such as safety equipment, optical lenses, electronic devices, and more.
Advantages:
- High strength and elasticity
- Excellent impact resistance
- Broad temperature tolerance
- Superior transparency with ease of coloring
- Tasteless, odorless, and safe for human contact, complying with health and safety standards
- Low molding shrinkage and excellent dimensional stability
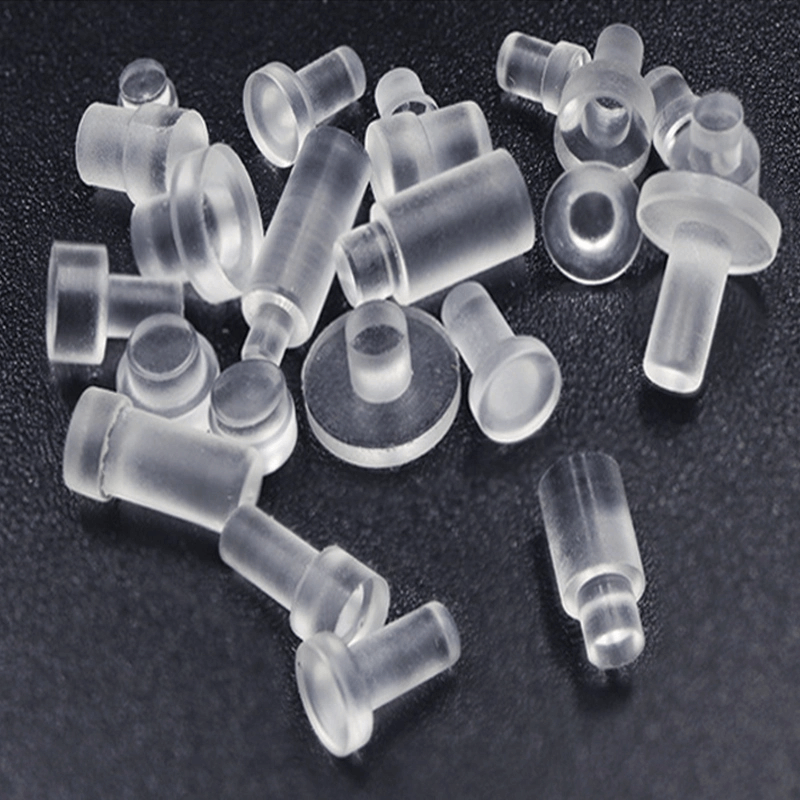
ABS (Acrylonitrile Butadiene Styrene)
Acrylonitrile Butadiene Styrene (ABS) is a high-strength, versatile engineering plastic commonly used in a wide range of commercial products.
Advantages:
- Excellent flexibility and durability, with resistance to breaking and ease of assembly
- Environmentally friendly: colorless, odorless, and non-toxic
- High flame retardancy, suitable for electronic applications
- Customizable color options (limited to solid colors)
- Commonly used in applications such as computer cases, television housings, switches, and set-top boxes
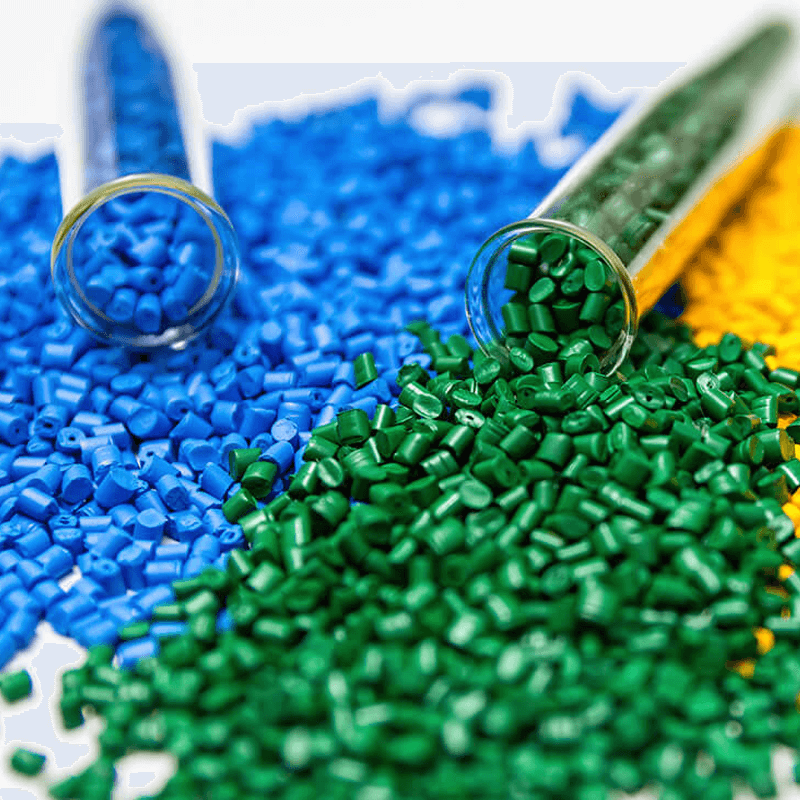
TPU (Thermoplastic Polyurethane)
Thermoplastic Polyurethane (TPU) is a durable, abrasion-resistant material that bridges the properties of rubber and plastic. It can be formulated to be either rigid or flexible, with a high flexural strength, making it ideal for applications like wheels and door panels.
Advantages:
- Wear and oil resistance
- Transparent with excellent elasticity
- Easy to dye and clean
- Environmentally friendly
- Hardness range from 70-98A, with temperature resistance from -50°C to 150°C
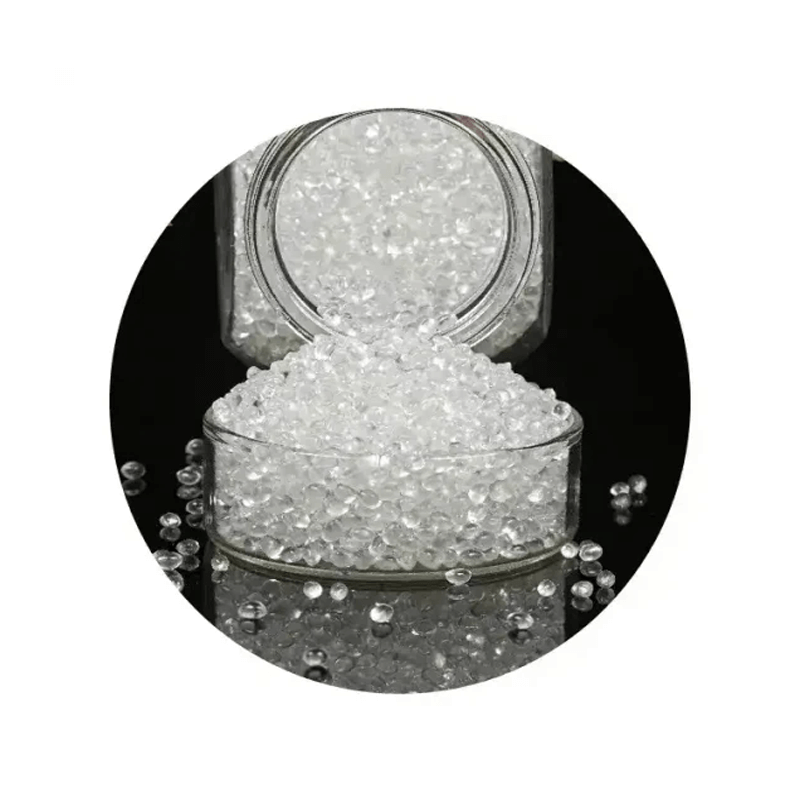
Customization Process
1. Submit your 3D design file or sample.
2. We create a customized product design (3-4 days).
3. 3D prototyping is done to confirm the product's structure (4-5 days).
4. Mold fabrication begins (15 working days).
5. Mold samples are produced for final approval (2-3 days).
6. Mass production begins.
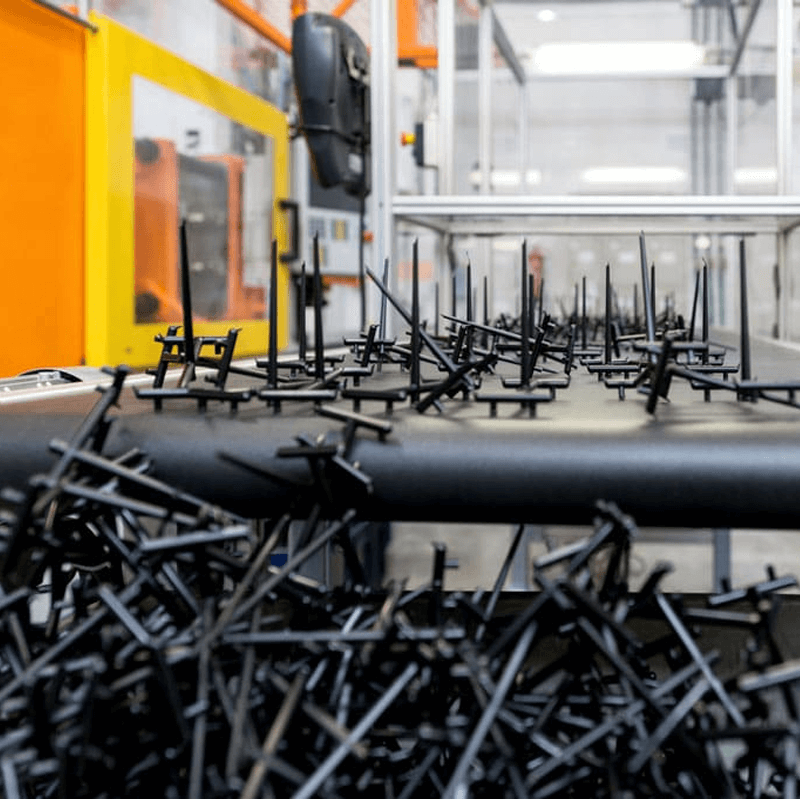
Injection Molding Process
Vacuum Plating
Vacuum plating involves heating and evaporating metal particles under high vacuum conditions, allowing them to adhere to a surface and form a thin metallic coating.
Pad Printing
Using imaging technology, the desired pattern is first printed onto a steel plate. A soft pad transfers the ink from the plate onto the object via a pad printing machine.
Water Transfer Printing
After soaking the decal in water, the pattern separates from its backing paper and transfers onto the object. This indirect printing method uses water as the medium for application.
IMD Process (In-Mold Decoration)
A decorative injection molding technique where designs are printed on a film, dried, and then molded into the desired shape during the injection process.
Fuel Injection (Paint Spraying)
Fuel injection, or paint spraying, is a surface coating process that enhances a product’s appearance with vibrant colors, offering added protection and extending product life.
Tolerance Guidelines
Tolerance ranges can vary depending on project requirements, material types, and the manufacturing equipment's capabilities. Below are typical tolerance ranges for different part sizes:
- Small Parts (less than 50 mm): Smaller parts generally allow for tighter tolerances, typically ranging from 0.05 mm to 0.2 mm.
- Medium Parts (50 mm to 200 mm): For medium-sized parts, tolerances are slightly wider, generally falling between 0.1 mm and 0.5 mm.
- Large Parts (greater than 200 mm): Larger parts typically require broader tolerances, usually ranging from 0.5 mm to 1 mm.
These values serve as general guidelines, and the actual tolerances may vary based on the specific project, material properties, and equipment capabilities. For each project, we work closely with our clients to assess and establish the most appropriate tolerance range based on their unique requirements and design constraints.
If your project demands specific or tighter tolerances, we will collaborate to adjust the parameters accordingly. Our objective is to ensure that all parts produced meet both design and functional specifications, providing high-quality results within the defined tolerance range.
FAQs
How Much Does Plastic Injection Molding Cost?
Learn how to lower the cost of manufacturing your custom parts by using our injection molding guide, which outlines key factors such as tooling, materials, and production that affect overall expenses.
Who Owns the Injection Mold?
Customers retain ownership of all custom tooling they develop. However, any reusable proprietary components created by the manufacturing partner (MP) remain the property of the MP. Custom tooling will be stored at the MP's facility for at least two years, with extensions available if needed. Transfers to different locations are available at the customer's expense.
What Happens if an Injection Molding Partner Exits Silfusion?
Should an injection molding partner leave Silfusion, we take responsibility for relocating all molds to another qualified manufacturing partner within our network, ensuring smooth production continuity and timely delivery.
What Is the Process After Placing an Order?
Once we receive your order, our manufacturing engineers will review the project scope. A dedicated case manager is assigned, and a suitable manufacturing supplier is chosen. We prepare a detailed DFM (Design for Manufacturing) report for your approval. After approval, tooling and mold production start. T1 samples are created and sent for approval, followed by mass production once approved.
What ISO Certifications Do You Hold?
We hold ISO 9001 and IATF 16949 certifications, demonstrating our commitment to maintaining strict quality control standards and meeting the high demands of our clients' industries.