About Our Tooling Manufacturing
As a leading name in tooling manufacturing, Silfusion stands out for its commitment to precision, quality, and innovation. We specialize in creating advanced tooling solutions for various industries, with a focus on the kitchenware sector. Our process combines cutting-edge technology, a skilled engineering team, high-quality materials, and a drive for continuous improvement to deliver tooling that meets the most rigorous standards of accuracy, durability, and performance.
At Silfusion, we don’t just manufacture tooling; we engineer solutions that enable our clients to elevate their production capabilities. Whether you need custom designs or complex manufacturing techniques, Silfusion is your partner for reliable, efficient, and cost-effective tooling production.
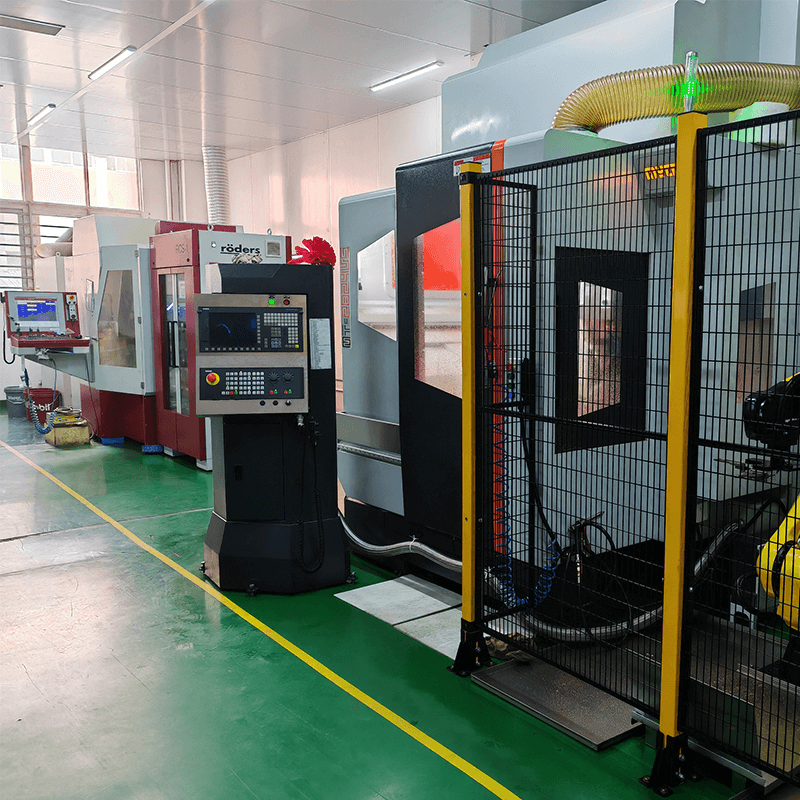
Comprehensive Tooling Capabilities
Our tooling manufacturing process covers the entire spectrum, from initial design concepts to final production. Our capabilities include:
- CNC Machining: Our high-precision CNC machines ensure the accurate manufacturing of tooling with tight tolerances, enabling us to create complex, intricate shapes without compromising quality.
- Mold Design and Development: With years of experience in designing molds, we understand the importance of functionality and longevity. Our molds are designed to withstand high production volumes while maintaining precision and consistency.
- Prototyping and Testing: We offer rapid prototyping and thorough testing to verify the design and functionality of each tooling project before full-scale production, ensuring optimal performance.
Quality Control Process for Tooling Manufacturing
At Silfusion, quality is at the heart of everything we do. Our comprehensive quality control process is designed to ensure that every tooling product meets the highest standards of precision and performance. We adhere to stringent international quality certifications, including ISO 9001:2015 and IATF 16949, to ensure that our tooling solutions are consistently reliable, durable, and efficient.
ISO 9001:2015 Certification: As an ISO 9001:2015-certified manufacturer, we follow a systematic approach to quality management, ensuring that each stage of the tooling manufacturing process is meticulously monitored and controlled. This certification guarantees that our products meet the highest quality standards and are continuously improved to exceed customer expectations.
IATF 16949 Certification: For clients in the automotive industry, our IATF 16949 certification provides additional assurance that our tooling meets the stringent requirements for automotive manufacturing. This certification highlights our commitment to quality, consistency, and precision in all aspects of our tooling production.
Step-by-Step Quality Control Process:
Material Inspection: We begin by conducting a thorough inspection of all raw materials, ensuring that only premium-grade materials are used in the production of tooling. This step helps prevent defects and ensures the longevity of the final product.
In-Process Monitoring: Throughout the manufacturing process, our team performs continuous in-process inspections to verify that the tooling is being produced to exact specifications. Using advanced measurement tools and techniques, we ensure that each component meets our stringent quality criteria.
Dimensional Accuracy Checks: After machining, we conduct precise dimensional accuracy checks using coordinate measuring machines (CMMs) and other advanced metrology tools. This step ensures that every part of the tooling adheres to the design’s exact measurements and tolerances.
Final Inspection and Testing: Once the tooling is fully assembled, we conduct a comprehensive final inspection. This includes functional testing to confirm that the tooling will perform as expected under production conditions. Any issues identified at this stage are promptly addressed to ensure the tooling is production-ready.
Customer Approval and Validation: Before delivery, we provide detailed reports of our quality control findings and offer samples or prototypes for customer approval. This final validation step ensures that the tooling meets the client’s exact needs and is ready for high-volume production.
By adhering to these rigorous quality control measures, we can confidently provide tooling solutions that meet the highest standards of precision, durability, and performance.
Why Choose Silfusion for Your Tooling Manufacturing Needs?
Selecting the right tooling manufacturer is critical to the success of your production process. Here are several reasons why Silfusion should be your go-to partner for tooling manufacturing:
Advanced Equipment and Technology
Silfusion is equipped with state-of-the-art manufacturing tools, including high-precision CNC machines, advanced CAD/CAM software, and 3D printing capabilities. These technologies allow us to achieve unmatched precision in our tooling processes, ensuring that every mold or tool we create meets the highest standards of quality.
- CNC Precision: Our CNC machines can achieve tolerances as tight as ±0.001 mm, allowing us to produce intricate designs and complex geometries with absolute precision.
- 3D Printing for Prototypes: With 3D printing, we offer rapid prototype development, allowing clients to evaluate designs in the physical space before committing to large-scale production.
- CAD/CAM Software Integration: Our software allows for the seamless transition from design to production, ensuring that the final product matches the client’s specifications down to the smallest detail.
Customized Design and Engineering Support
At Silfusion, we believe that every client’s needs are unique, which is why we offer custom design services tailored to each project. Our team of experienced engineers collaborates closely with clients to understand their specific requirements and design tooling that aligns perfectly with their production goals.
- Design Collaboration: We work with your team to understand your product specifications, production volumes, and material requirements to develop the most efficient tooling design.
- Engineering Expertise: Our engineers are highly skilled in optimizing designs for manufacturability, ensuring that your tooling not only meets your production needs but also contributes to cost savings and reduced lead times.
High-Quality Materials and Manufacturing Standards
Tooling quality starts with the materials used. At Silfusion, we source only the highest-grade materials to ensure that our tools are both durable and efficient. This includes premium-grade steels, wear-resistant alloys, and heat-treated components that enhance the lifespan and reliability of your tooling.
- Premium-Grade Materials: We use materials such as H13 tool steel, P20 mold steel, and other high-performance alloys to create tooling that can withstand high-pressure production environments without degradation.
- Strict Quality Control: Every tool we manufacture undergoes rigorous quality checks throughout the production process. From material selection to final inspection, we adhere to ISO 9001-certified processes that guarantee the reliability and durability of your tooling.
Manufacturing Efficiency and Production Cycle Optimization
Efficiency is key in today’s competitive manufacturing environment. At Silfusion, we optimize the production cycle by employing lean manufacturing principles, which minimize waste and maximize productivity. Our streamlined processes reduce lead times, helping you get your products to market faster without sacrificing quality.
- Lean Manufacturing: By applying lean principles, we eliminate unnecessary steps and focus on value-added activities, ensuring faster turnaround times and reduced costs.
- Production Cycle Management: Our comprehensive project management approach ensures that every stage of tooling production, from design to delivery, is handled efficiently. This allows us to meet tight deadlines while maintaining the highest standards of quality.
Cost-Effectiveness and Long-Term Return on Investment
While tooling manufacturing may require a significant upfront investment, Silfusion’s precision tooling offers a high return on investment (ROI) in the long run. Well-designed tooling reduces production costs by enabling faster cycle times, reducing material waste, and minimizing the risk of defects.
- Reduced Production Costs: Our precisely engineered tooling helps manufacturers cut down on cycle times, reducing labor and material costs while boosting output.
- Reusability and Durability: The high durability of our tooling means fewer replacements and less downtime, which translates to significant cost savings over the product’s lifecycle.
Technological Innovation and Continuous Improvement
Innovation is at the core of Silfusion’s business philosophy. We constantly explore new materials, manufacturing techniques, and technologies to improve our tooling solutions. Our focus on continuous improvement ensures that we stay ahead of industry trends and offer our clients the most advanced, efficient tooling on the market.
- Advanced Processes: We integrate cutting-edge technologies such as laser cutting, EDM (Electrical Discharge Machining), and automated milling into our production processes to enhance accuracy and reduce lead times.
- R&D Investment: Our ongoing investment in research and development ensures that we are always improving the quality and performance of our tooling products.
Industries We Serve
Silfusion’s tooling solutions are used across a range of industries, with a particular focus on kitchenware, medical devices, automotive components, and consumer electronics. Each industry has unique requirements, and we tailor our tooling designs to meet those specific needs.
Kitchenware
Our tooling for kitchenware products ensures high precision and repeatability, whether for plastic injection molding, silicone molding, or metal stamping.
Food Grade Silicone Cake Mold with Custom Logo Factory
Characteristics:
Item | Details |
Place of Origin | Xiamen, China |
Brand Name | OEM |
Size | Custom |
Logo | Custom Logo |
Package | OPP bag or customized packing |
Color | Accept customized color |
Sample | Available |
Certification | ISO, FDA, ROHS |
Material | Food Grade Silicone |
Lead Time | 20~25 days |
OEM High Quality Silicone Lids for Bowl Kitchen Application Factory
Characteristics:
Item | Details |
Place of Origin | Xiamen, China |
Production Capacity | 500,000 pcs per month |
Custom Order | Accepted |
Brand Name | OEM |
Material | Food-grade silicone |
Color | Any Pantone color |
Temperature Range | -40℃ to +230℃ |
Logo Printing | Customized logo available (Laser or Pad Printing) |
Application | Silicone lids/covers for food containers |
MOQ | Small orders accepted |
Size | Custom sizes available |
Shape | Custom shapes available |
Packing | According to your specific requirements |
Certifications | ISO, RoHS, FDA |
Silicone Vegetable Preservation Bag Factory
Basic Information
Place of Origin :Xiamen, China
Weight Tolerance :< ±5% (Including)
Type: Storage Bags
Applicable Space: Kitchen
Product :Silicone Food Bags
Shape :Custom
Capacity: 500ml / 1000ml / 1500ml
Feature: Sustainable, Folding, Stocked
Brand Name :OEM
Name :Silicone Reusable Food Storage Bag
Lifespan :Typically more than 3,000 uses, depending on usage
Material :100% Food Grade Platinum Silicone
Usage: Food Storage, Article Reserves, Sous Vide, Freezing, Lunch Bag, Baby
Function :Reusable, Ziplock Fresh, Standing Up, Collapsible, Roll Up, Leakproof
Custom :Logo, Package, Color, and Design can be customized
Certificate :BSCI, BPA Free, ISO9001
Logo: Print, Embossed, Laser
Application: Oven, Refrigerator, Dishwasher, Outdoor
Medical Devices
In the medical field, precision and cleanliness are paramount. We produce tooling that meets strict medical-grade standards, ensuring the highest levels of safety and hygiene.
Silicone Medical Face Mask Factory
Overview Silicone Medical Face Masks are designed with a focus on hygiene and safety during production. Manufactured using Liquid Silicone […]
Custom Silicone Laryngeal Mask
Hygiene is a critical consideration in the production of medical products. For medical face masks, Liquid Silicone Rubber (LSR) molding […]
Silicone Gasket Manufacturer
Silicone Gasket is a flexible, heat-resistant sealing component designed to prevent leaks and maintain airtight or watertight seals in various […]
Automotive Components
Our tooling for automotive parts is built to withstand the rigors of high-volume production, delivering consistent results with each cycle.
Consumer Electronics
For electronics, we offer tooling solutions for intricate, detailed parts that require high levels of accuracy and precision.
Partnering with Silfusion for Your Tooling Needs
At Silfusion, we understand that high-quality tooling is the foundation of successful manufacturing. By choosing us, you gain access to industry-leading expertise, cutting-edge technology, and a commitment to innovation. We don’t just manufacture tools; we provide solutions that help you achieve your production goals faster, more efficiently, and at a lower cost.
Let Silfusion be your trusted partner in tooling manufacturing—contact us today to learn how we can help your business thrive.