What Is Liquid Silicone Rubber (LSR) Injection Molding?
Liquid Silicone Rubber (LSR) molding is a sophisticated manufacturing process used to produce high-quality silicone products. This method involves two primary components: Part A (the base matrix) and Part B (the catalyst). These components are precisely injected into a closed mold, where they combine and begin to cure, taking on the exact shape of the desired part. Upon completion of the curing process, the machine ejects the finished silicone product.
The LSR molding process is ideal for large-scale production due to its fully automated operations, which are conducted in an ISO Class 8 clean room environment. This method is highly suitable for producing silicone products that meet stringent food-grade and medical-grade standards.
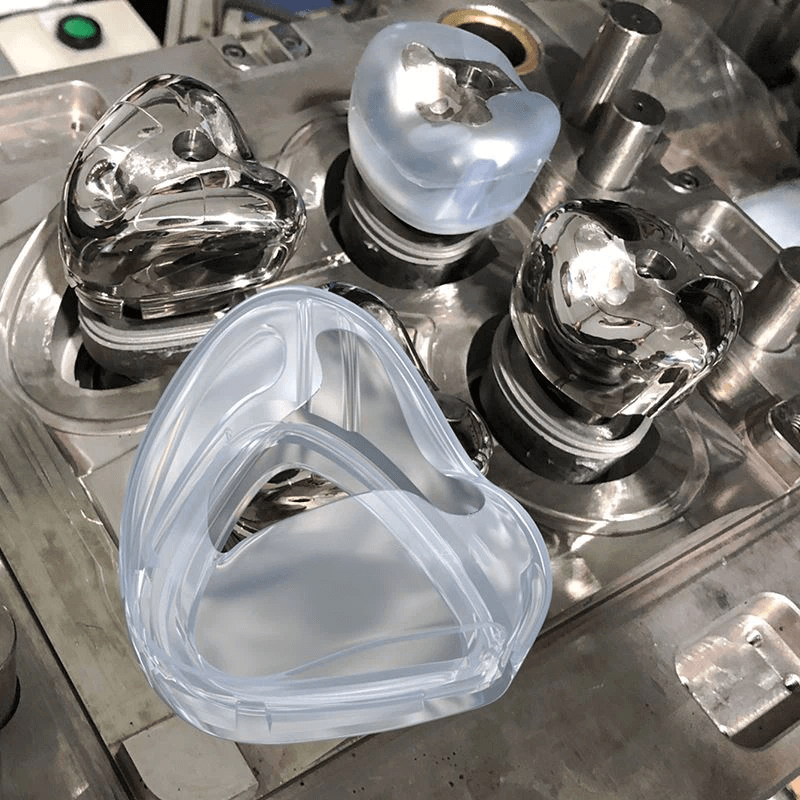
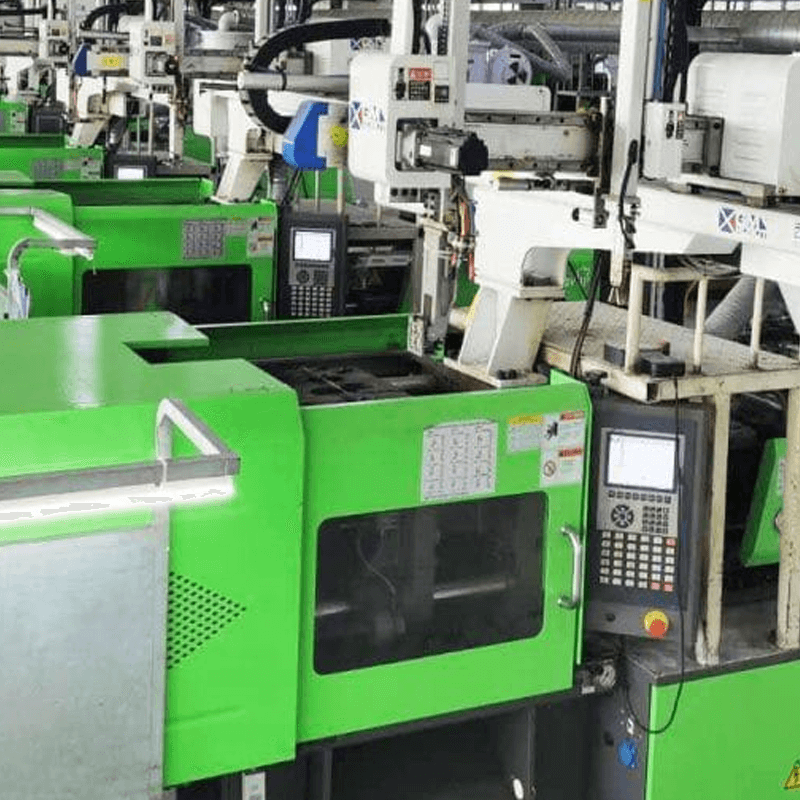
Our Injection Molding Advantages
Silfusion provides comprehensive injection molding services to global clients, leveraging our team of skilled and diverse designers and engineers to deliver cost-effective solutions. Our robust management system guarantees the reliable delivery of high-quality products, tailored to meet your need for swift turnaround times.
Exceptional Quality
Rapid Turnaround
Versatile Applications
Cost Efficiency
Characteristics of Liquid Silicone Rubber
Liquid silicone rubber (LSR) has been a preferred material for manufacturing rubber parts due to its advantageous raw material properties. The injection molding of LSR enhances productivity and consistency in part quality, supports high-volume production, and simplifies both production and processing.
Thanks to its distinctive properties, LSR is an ideal choice for creating specialized parts and applications. Here are some key characteristics of LSR:
- Biocompatibility
LSR exhibits excellent compatibility with body fluids and human tissue, making it suitable for medical applications. It is resistant to bacterial growth and will not corrode or stain other materials. Additionally, LSR is odorless and tasteless, allowing it to meet stringent FDA guidelines. It can be sterilized using various methods, including e-beam, ethylene oxide (ETO), gamma radiation, and steam autoclaving.
- Durability
LSR's ability to withstand high temperatures makes it ideal for manufacturing components that are exposed to extreme conditions, such as those found near engines or under the hood of vehicles. Unlike plastic injection molded components, which can melt under high temperatures, LSR parts are fire-resistant and maintain their integrity.
- Chemical Resistance
LSR is highly resistant to oxidation, water, and various chemical solutions, including alkalis and acids, ensuring its durability in challenging environments.
- Temperature Resistance
LSR maintains its properties across a wide temperature range, outperforming many other elastomer materials in high and low temperatures.
- Mechanical Properties
LSR offers exceptional elongation, high tensile and tear strength, and good flexibility and toughness. Its hardness can be customized within a range of 5 to 80 Shore A, providing versatility for various applications.
- Electrical Properties
With superior insulating properties, LSR is an excellent choice for electrical applications. It performs reliably across a broad temperature spectrum compared to traditional insulating materials, making it suitable for demanding electrical environments.
These characteristics make LSR a versatile and reliable material for various applications, from medical devices to automotive components and beyond.
Why Choose Silfusion for Your Silicone Injection Molding Services?
- Accelerated Testing and Production
- State-of-the-Art Facilities
- Cost-Effective Durability
- Expert Engineers
- Unlimited Capacity
- Rapid Delivery
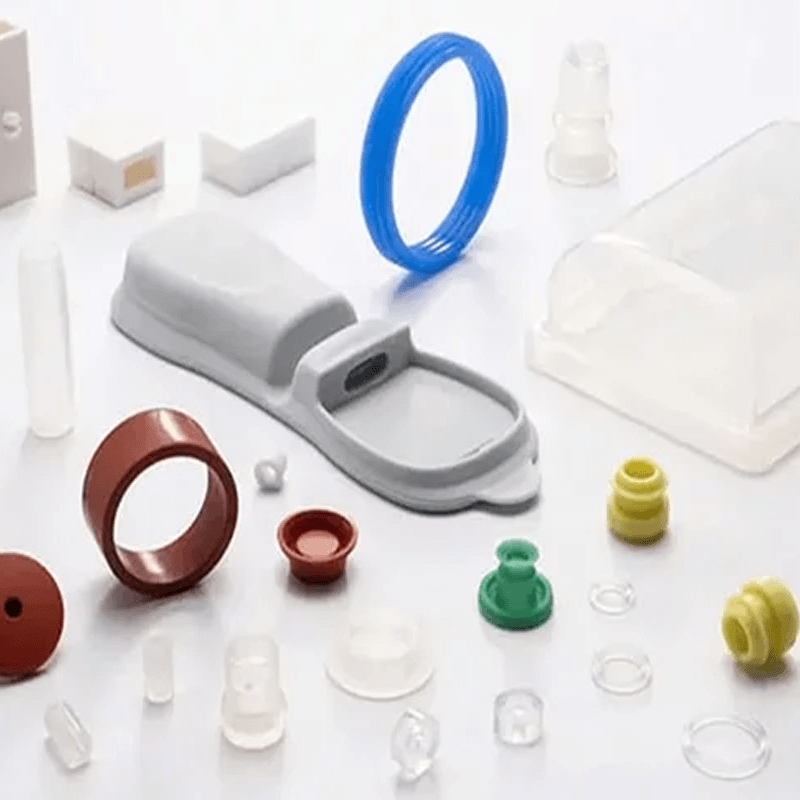
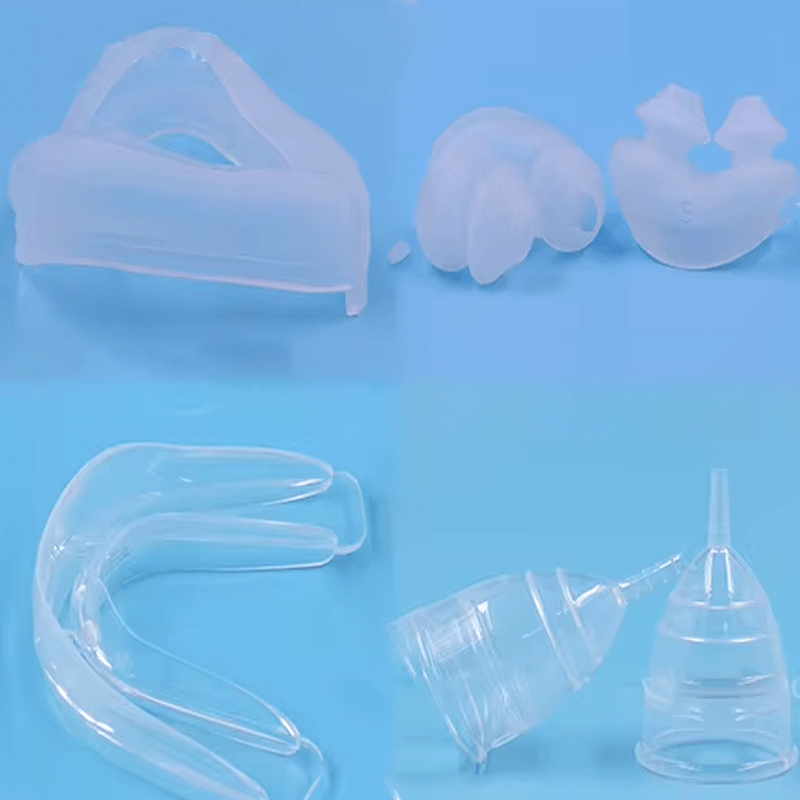
LSR Parts Production
At Silfusion, we offer a range of advanced options for LSR (Liquid Silicone Rubber) part production. We meticulously assess each project to select the most suitable LSR injection molding technology, including LSR, LSR two-shot, LSR multi-shot, or LSR overmolding, tailored to your specific needs.
Our cutting-edge facility is both climate-controlled and exceptionally clean. With fully automated LSR, LSR two-shot, multi-shot, and overmolding production cells, human contact is minimized, ensuring high levels of cleanliness and precision.
Silfusion operates an ISO Class 8 cleanroom equipped with both single-shot and over 12 LSR molding machines. Additionally, we perform a range of post-molding value-added processes to ensure the highest quality and functionality of your parts.
Related Custom Solutions from Silfusion
Single-shot molding: In this molding process, only one LSR material is used for injection molding parts.
Multi-shot molding: LSR is combined with two or more polymers or a polymer and substrate in this process for more complex components.
Overmolding: In overmolding, the liquid silicone rubber is molded around a substrate or finished component.
Micromolding: This injection molding process produces tiny, complex parts, typically with a shot weight of less than 1 gram.
Hygienic molding: LSR parts are produced in a clean, hygienic environment that are highly-controlled to various levels, such as white rooms or more stringent ISO cleanrooms with various classifications.
Quality Inspections and Finishing Options
When requesting a quote for your silicone rubber components, you can select from a range of quality inspection and finishing options tailored to your specific application requirements.
Available Quality Inspections for On-Demand Manufacturing Orders:
- Design for Manufacturability (DFM) Feedback: Comprehensive evaluation and recommendations to optimize your design for efficient and cost-effective manufacturing.
- Scientific Molding Process Development Report: Detailed documentation of the scientific approach used in molding process development to ensure consistency and performance.
- In-Process CMM Inspection and Machine Monitoring: Continuous monitoring and inspection using Coordinate Measuring Machines (CMM) to ensure precision and adherence to specifications throughout the production process.
- First Article Inspection (FAI) and Process Capability Report: Initial inspection of the first produced part along with a detailed report on process capability, including Failure Mode and Effects Analysis (FMEA), to validate that the manufacturing process meets all quality standards.
These quality control measures are designed to guarantee that your silicone rubber parts meet the highest standards of performance and reliability.
Application Industries of Silicone Injection Molding
Silicone injection molding is crucial across several industries due to its unique properties:
Medical and Healthcare
Used for biocompatible components like seals and medical devices that must endure sterilization.
Automotive
Produces high-performance parts such as engine seals and gaskets, resistant to extreme temperatures and chemicals.
Consumer Electronics
Creates flexible and durable components like keypads and protective covers, offering excellent insulation and temperature resistance.
Food and Beverage
Provides safe, heat-resistant components like kitchen utensils and molds that meet strict health standards.